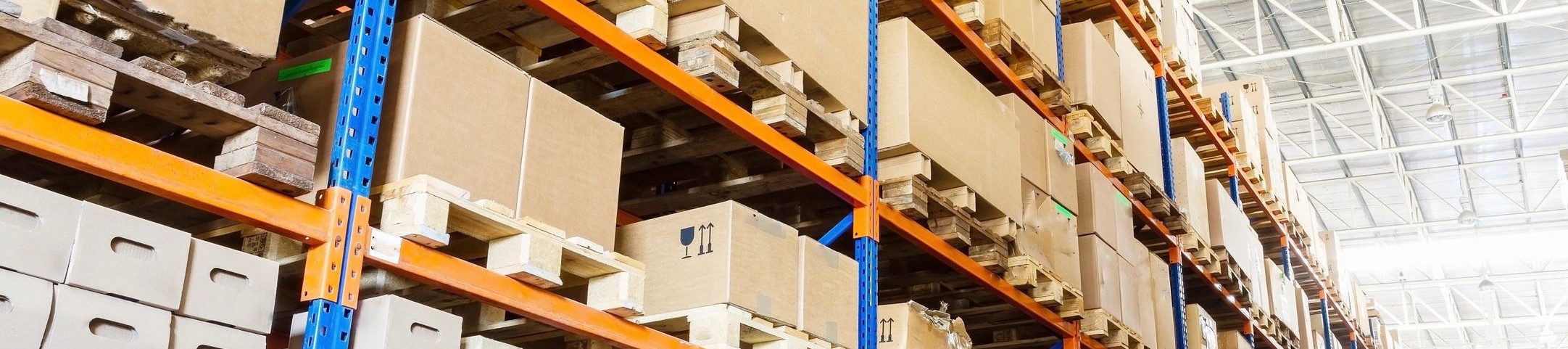
Lean Supply Chain
Material availability - in the right quantities, at the right place, at the right time and at the right cost - can be enormously challenging in today's environment. We will design and implement the right material supply and replenishment system for your business.
Kanban systems use robust replenishment signals (generally physical signals) to drive replenishment based on actual usage. Kanban systems have enormous flexibility and responsiveness, and can free up your planners, buyers and inventory specialists from managing the majority of items. This will enable your team to focus their effort managing the most critical supplies and inventory items.
With a Lean Supply Chain, we can help to eliminate shortages, reduce inventory and management effort.
Our integrated approach allows you to link supply to demand throughout your business:
- At the manufacturing workstation:
- short replenishment times
- quantities to match supplier container size
- avoid the need for transactions wherever possible
- material presentation for disciplined usage and replenishment
- visual replenishment signals easy to use
- At the shop floor material supply area:
- Supplier containers
- Inspected or "trusted' quality material
- kanban quantities to cover variation in usage and supply
- simple transactions onto the floor
- clear, visual signals for replenishment
- At machine cells supplying downstream processes:
- machine run quantities calculated to accommodate machine capacity, setup times, setup families and container sizes
- simple, rule-based boards to control sequence and grouping of orders at each cell
- multiple-card kanban system to enable minimal on-hand inventory even in environments with large machine run quantities
- consumption quantities sized to accommodate variation and replenishment time
- At the raw material stockroom:
- Balance the strengths of physical and electronic kanban systems depending upon your business situation:
- Physical kanban:
- Simple, easy-to-follow signals
- Signals work even if system inventory is inaccurate
- Kanban cards can contain additional information and barcodes to simplify transactions
- Electronic kanban:
- Scalable, feasible for an unlimited number of items.
- Allows random location system to save warehouse space
- Calculate inventory quantities to accommodate variations in usage and replenishment, seasonality and forecast trends
- Permits automatic transmission or posting of replenishment signals
- Physical kanban:
- Apply multiple-card signaling techniques to minimize on-hand inventory, even with long lead-times
- Balance the strengths of physical and electronic kanban systems depending upon your business situation:
- At the Finished Goods Warehouse or Distribution Center:
- Apply physical or electronic kanban methods
- Accommodate special-order or infrequently-used parts, shared items
- Calculate inventory quantities to accommodate variations in usage and replenishment, seasonality and forecast trends
- Apply multiple-card signaling techniques to minimize on-hand inventory, even with long lead-times
- Link signals and kanban quantities to your suppliers' and manufacturing facilities' lead-time and inventory policies
- At your suppliers and subcontractors:
- Define and negotiate terms to manage replenishment, demand variation, finished, in-process and raw inventory, and financial exposure.
- Calculate inventory requirements and exposure
- Define procedures to control and ensure performance.
Contact us to learn more about how we can help you transform your supply chain.