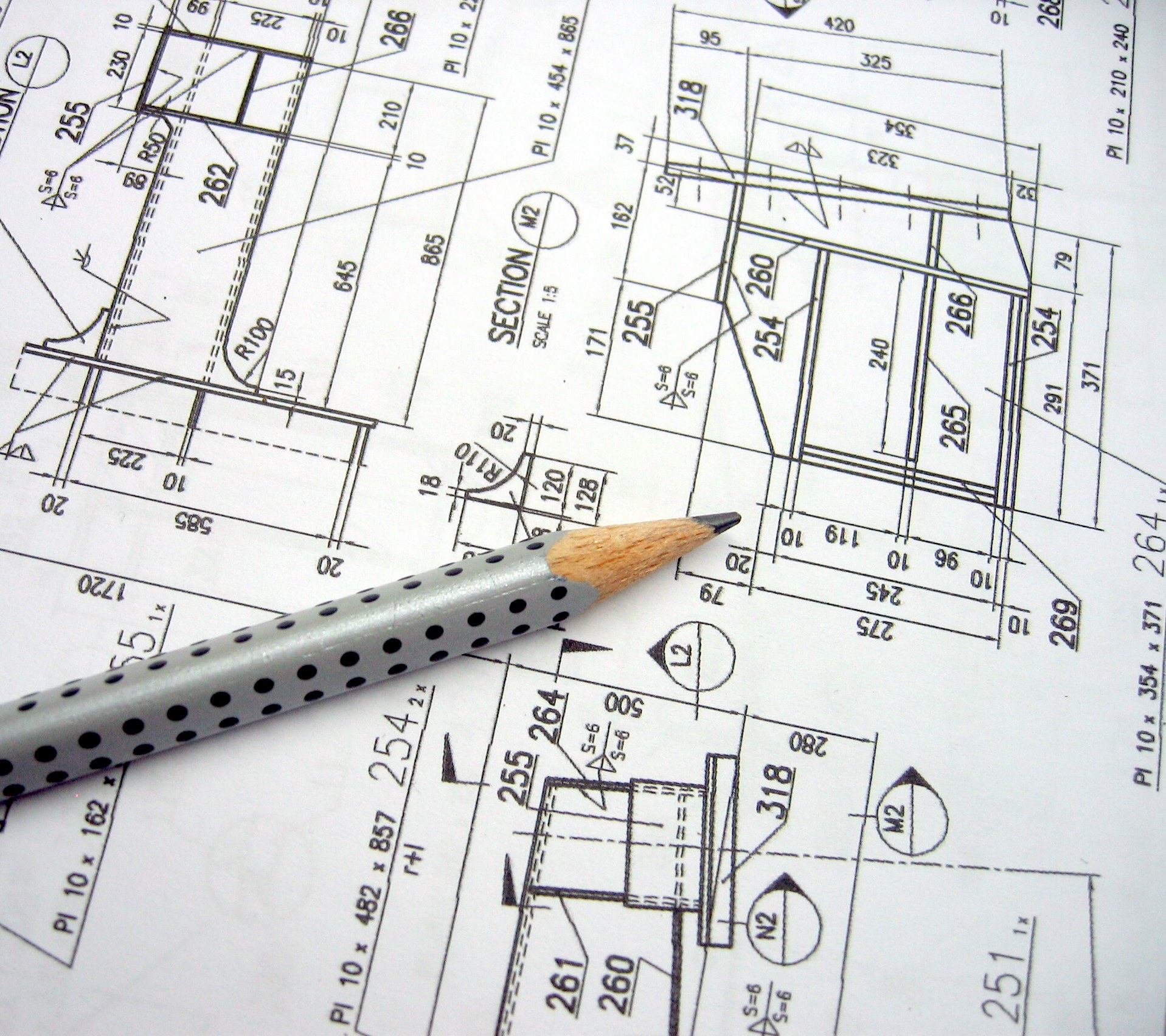
The same principles that apply on a manufacturing shop floor apply to all work processes - particularly where work moves between multiple individuals. We've demonstrated remarkable successes in engineering design environments across the globe, typically reducing lead-time by 50-90%.
- Establish product families
- Based on service type, complexity and work content
- Establish process flows for each product family
- Identify immediate process flow changes to optimize process
- Define work and time for each process (SOWs)
- Identify waste reduction projects
- Calculate required resources
- how many people we need of each skill set
- on average, and based on likely order mixes
- accommodate growth, technology and market changes
- Establish cells with common processes and similar work times
- "Standard", "Medium", "Complex" cells
- Allow faster products to flow through without being held up behind a slow-moving "complex" product
- Prevent workers engrossed in "complex" products being interrupted by "standard" products
- Establish IPKs and operating rules
- minimize queues between workers
- process orders first-in-first-out
- individuals "flex" or move between tasks in response to backlog signals
- managers apply daily audit and follow-up routines
- resolve "on hold" orders
- Daily routines to optimize productivity
- enable workers to focus in productive blocks of time without interruption
- meeting schedules
- routines to handle interruptions
- phone and email techniques
- Create Block Diagram
- a conceptual layout of the process
- Design new layout
- enable communications
- simplify management
Contact us to learn more about how we can help you transform your service-based business.